Porosity in Welding: Identifying Common Issues and Implementing Finest Practices for Avoidance
Porosity in welding is a prevalent concern that usually goes unnoticed up until it triggers considerable problems with the honesty of welds. In this discussion, we will discover the key elements contributing to porosity development, analyze its destructive results on weld efficiency, and discuss the ideal practices that can be adopted to decrease porosity event in welding processes.
Usual Root Causes Of Porosity
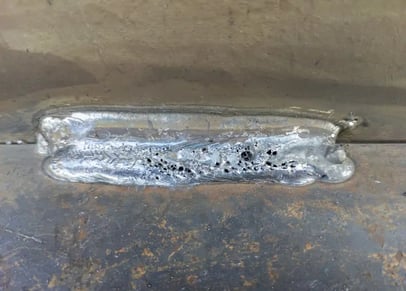
Making use of dirty or wet filler products can present contaminations into the weld, adding to porosity problems. To minimize these typical causes of porosity, comprehensive cleansing of base metals, correct protecting gas choice, and adherence to optimal welding parameters are important techniques in achieving top quality, porosity-free welds.
Impact of Porosity on Weld Top Quality

The existence of porosity in welding can dramatically endanger the architectural integrity and mechanical residential or commercial properties of welded joints. Porosity develops gaps within the weld metal, deteriorating its total toughness and load-bearing capability.
Among the key effects of porosity is a decline in the weld's ductility and strength. Welds with high porosity degrees have a tendency to exhibit lower effect toughness and reduced capacity to warp plastically prior to fracturing. This can be especially worrying in applications where the bonded components undergo dynamic or cyclic loading problems. Additionally, porosity can impede the weld's capacity to properly transmit pressures, resulting in premature weld failing and potential safety and security risks in vital structures.
Finest Practices for Porosity Avoidance
To improve the architectural integrity and top quality of bonded joints, what certain measures can be carried out to reduce the occurrence of porosity throughout the welding process? Utilizing the correct welding strategy for the details product being welded, such as changing the welding angle and weapon setting, can further prevent porosity. Normal inspection of welds and prompt removal of any concerns identified throughout the welding procedure are vital methods to stop porosity and produce high-grade welds.
Significance of Appropriate Welding Strategies
Applying appropriate welding techniques is vital in ensuring the architectural integrity and quality of welded joints, developing upon the foundation of effective porosity prevention procedures. Welding methods straight affect the general stamina and longevity of the bonded framework. One crucial element of proper welding methods is preserving the appropriate heat input. Too much warmth can cause enhanced porosity as a result of the entrapment of about his gases in the weld swimming pool. On the other hand, insufficient warmth might cause insufficient combination, developing prospective weak factors in the joint. Additionally, using the appropriate welding specifications, such as voltage, existing, and take a trip rate, is vital for accomplishing audio welds with very little porosity.
Moreover, the selection of welding process, whether it be MIG, TIG, or stick welding, need to line up with the particular demands of the project to ensure ideal results. Appropriate cleansing and prep work of the base metal, as well as selecting the best filler product, are also crucial parts of efficient welding methods. By sticking to these best practices, welders can reduce the risk of porosity formation and produce top notch, structurally audio welds.
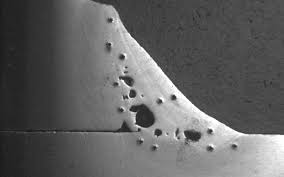
Evaluating and High Quality Control Steps
Quality assurance measures play an essential function in verifying the honesty and reliability of bonded joints. Checking treatments are Discover More Here necessary to detect and prevent porosity in welding, ensuring the toughness and sturdiness of the last item. Non-destructive testing techniques such as ultrasonic screening, radiographic screening, and visual inspection are commonly utilized to recognize possible defects like porosity. These strategies enable the evaluation of weld top quality without endangering the integrity of the joint. What is Porosity.
Post-weld inspections, on the other hand, assess the final weld for any type of issues, including porosity, and validate that it satisfies defined requirements. Implementing a comprehensive high quality control strategy that includes thorough screening treatments and examinations is critical to decreasing porosity concerns and making certain the total high quality of bonded joints.
Conclusion
In verdict, porosity in welding can be an usual concern that impacts the top quality of welds. By determining the usual reasons of porosity and executing finest methods for avoidance, such as correct welding methods and testing actions, read what he said welders can make sure excellent quality and reliable welds. It is crucial to focus on prevention approaches to decrease the event of porosity and keep the honesty of bonded frameworks.